Application and Improvement of Rotary Vibration Screen in Ceramic Slurry
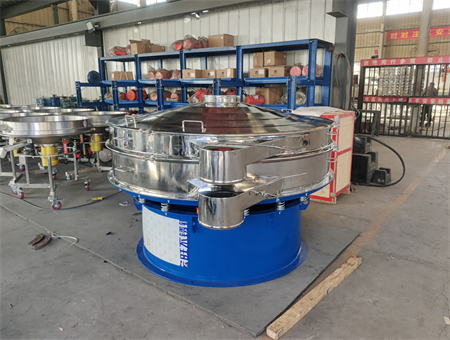
Through continuous innovation and technological improvement, the screening effect of
rotary vibrating sieve in the ceramic industry has been recognized by a large number of customers. The rotary vibrating screen has the following improvements in practical applications, targeting the characteristics of the ceramic industry:
1、
Improvement of Rotating Vibration Screen Motor
Due to the
vibration motor operating in a high-temperature continuous operating environment, it is easy to cause the lubricating oil added to the bearings to flow into the wire package, forming a short circuit and burning the motor. Therefore, sealing rings (double seals) have been installed on both the upper and lower end covers to prevent the lubricating oil from flowing into the wire package and burning the motor. Large clearance bearings (C3 bearings) are also used on the motor bearings, extending the service life of the bearings.
2、
Preventing the rotation of vibrating bodies
To prevent the looseness and rotation of the upper vibrating body from causing damage to the vibrating body, there is a 15 ° slope at the edge of the screen plate, also known as the bundling ring, and a sealing rubber pad is installed. As the slope of the bundling ring is relative to the slope of the screen plate edge, it is easy to get more tightly clamped in the fastening bundling ring to prevent the rotation of the vibrating body.
.jpg)
3、 Discharging impurities from ceramic slurry
In order to ensure that impurities in the ceramic slurry are easier to be discharged, a rubber skin is installed on the metal baffle at the discharge port to make the rubber skin tightly adhere to the sieve, ensuring that impurities are discharged quickly. This reduces the residence time of impurities on the sieve, increases the permeability of the slurry, and increases the processing capacity of the slurry.
4、 Extend the service life of the screen
In the ceramic industry, direct impact of mud on the screen mesh can easily cause damage to the screen mesh. To avoid this situation, a buffer valve is installed at the feed inlet to reduce the impact of mud on the screen mesh surface, extend the service life of the screen mesh, and save usage costs.
5、 Improving the work environment
To prevent the splashing of ceramic slurry, the height of the upper screen frame has been increased, improving the operating environment.